Terminology
- Thermal Spraying without fusion process (Cold spraying)
- Thermal Spraying with simultaneous fusion process
- Thermal Spraying with subsequent fusion process
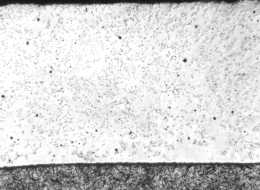
Fused coating
Thermal Spraying without fusion process (Cold spraying)
Processes
- Thermal Powder flame spraying
- Arc spraying / Wire flame spraying
- Atmospheric plasma spraying (APS)
- Plasma spraying under partial vacuum (VPS)
- High speed flame spraying (HVOF)
- High speed flame spraying (Detonation-Gun)
Thermal Powder flame spraying
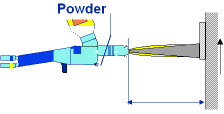
Flame spraying
The powder is fed in a flame (Acetylene and oxygen)
The molten powder is sprayed on the workpiece surface.
Arc spraying
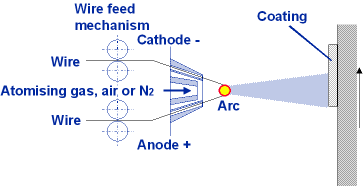
Arc spraying torch
The consumables are two solid or metal core wires. They are fed in the centre of
a spray jet (air or nitrogen).
Between these two wires of good electrical conductivity is stroked an arc for
melting the consumables.
The molten metal is atomised and sprayed on the workpiece surface.
Atmospheric plasma spraying (APS)
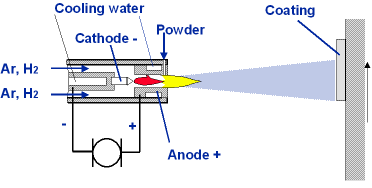
Plasma torch
In technical usage the term plasma means the ionisation, and in some cases the
dissociation, of a gas used to conduct electricity. It has been described as
the fourth state of matter, as it does not conform to the other three.
The plasma state is created by striking a high-powered arc between a cathode and
an anode, inside a cooled torch.
The molten powder is sprayed on the workpiece surface.
High speed flame spraying (HVOF)
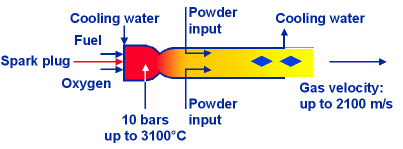
HVOF
Fuel or fuel gas and oxygen are mixed in a combustion chamber.
The combustion is stable and uniform.
It creates a constant pressure.
Particle velocity is directly related to chamber pressure.
The exit nozzle is sized and shaped to create a supersonic jet and to maintain a
low-pressure area where the powder is injected.
The molten powder is sprayed on the workpiece surface.
Procedure for new parts (see also instructions from the equipment manufacturer)
- Machining
- Degreasing
- Masking
- Grit blasting
- Brushing, if necessary
- Degreasing, if necessary
- Spraying
- Machining
Procedure for Repairing (Thermal Powder flame spraying)
- Degreasing and cleaning
- Mechanical preparation
- Preheating I ( 80 - 100°C), cast iron 200 - 300°C/2h
- Grit blasting
- Preheating II (Iron base alloys: 50°C, Aluminium-/Copper alloys: 150°C)
- Spraying
- Machining
Safety: Powder flame spraying, Arc spraying, HVOF and Plasma spraying
see chapter safety
Thermal Spraying with fusion process
Processes
- Thermal Powder flame spraying
- Laser spraying
- PTA
Thermal Powder flame spraying with simultaneous fusion process
The powder is fed in a flame (Acetylene and oxygen)
The molten powder is sprayed on the workpiece surface and fused simultaneously.
Thermal Powder flame spraying with subsequent fusion process
The powder is fed in a flame (Acetylene and oxygen)
The molten powder is sprayed on the workpiece surface and fused subsequently.
Safety: Powder flame spraying
see chapter safety
Laser spraying
CO2 Lasers are the most traditional high power lasers and are available in different power levels.
The high wavelength results in a relative low absorption of the laser beam by metals. A surface
pre-treatment is common for improving absorption.
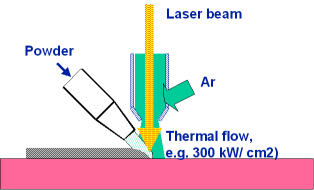
Laser spraying
Solid state lasers, e.g. Nd:YAG lasers operate at a lower wavelength which improves the absorption
characteristics. However, these lasers operate at significantly lower electrical/optical efficiency
which makes the equipment bulky and costly to run.
High power diode lasers (HPDL) were introduced recently. They represent the newest generation
of high power lasers for material processing:
- Welding
- Coating and surface treatment
- Polymer welding
- Brazing and soldering
They are available at maximum 6 kW. However, the lower wavelength improves the absorption
characteristics of the laser beam. Due to the very high electrical/optical efficiency,
HPDL equipments are remarkably smaller in size than other lasers with similar kW level.
The poor beam quality is not a key factor when using HPDL laser for coating and surface hardening.
Coating materials
- Unalloyed and alloy steel
- Self-fluxing alloys
- Stainless steels
- Nickel and nickel based superalloys (Inconel 625, Alloy 59, NiCr, NiCrAl, NiCu, etc.)
- Cobalt alloys (Stellit 6, 12, 21)
- Copper alloys (Aluminium bronze)
- Carbide containing alloys and composites
Safety: Laser spraying
Contact the equipment manufacturer
PTAW
The Plasma Transferred Arc Welding process is at the same time a thermal spraying and a
welding process.
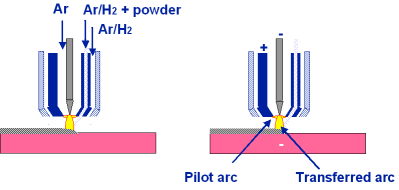
PTAW torch
A smooth high-energy electrical arc is created within the torch head (anode and cathode)
and between the torch and the base metal. Powdered alloy is fed into the plasma arc by an inert
gases. The powder is melted and accelerated toward the substrate, forming a liquid puddle
on the surface of the workpiece.
The coating metallurgically bonds to the substrate.
PTAW has the following features:
- High deposition efficiencies
- Low dilution factor (generally less than 10%)
- Metallurgical bonding between the coating and the workpiece.
The degree of dilution is dependent upon substrate type and mass and welding parameters.
A low dilution factor ensures that the wear surfacing alloy achieves the required
wear resistance properties in one pass. This can be significant in terms of economics
when compared to other arc welding processes.
The metallurgical bonding is important when resisting against heavy wear is necessary.
Safety: PTAW (Arc welding)
see chapter safety
For further information, on-site training, technical advise or project management, please do not hesitate to
contact us.
|