Welding of common steels
Unalloyed steels
Unalloyed steels are prone to cold cracking. In many cases preheating is
required to ensure good weldability.
Preheating:
C < 0.2 %: |
|
without preheating (up to 30 mm thickness) or 100°C against humidity |
C: 0.2 to 0.5 %: |
|
preheating temperature 100 to 300°C |
C > 0.5 %: |
|
preheating temperature 300 to 350°C |
Possible post-weld treatments:
- Stress relieving
- Normalising
Low alloy steels
Low alloy steels are prone to cold cracking. In many cases preheating is
required to ensure good weldability.
Preheating:
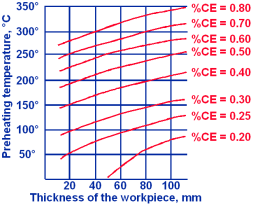
Séférian diagram
Possible post-weld treatments:
- Stress relieving
- Quenching and tempering
Fine-grained steels
Fine-grained steels are prone to cold cracking due to hydrogen absorption. They
should be preheated slightly and welded with a relatively low specific energy,
to reduce the heat-affected zone.
Preheating: in function of steel, generally 100°C (max. 200°C)
Welding: with moderate energy input per unit of length
Post-weld treatment: usually not necessary
Manganese steels
Austenitic manganese steels with a manganese content of 14% (Hadfield steels)
have a tendency to form brittle precipitates in the form of carbides.
It is essential to weld them without preheating, even with additional cooling,
and to keep the specific heat input low.
Preheating: none (cooling may be used if needed)
Possible post-weld treatments: none
Austenitic stainless steels
Austenitic stainless steels are prone to hot cracking and so should be cleaned
and welded with a low specific energy
Weldability: Watch for formation of chromium carbide at grain interface, if
carbon content is higher then 0.04%
Preheating: Usually none
Filler metal: % C = max. 0.04 %
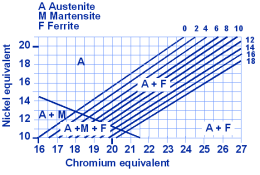
DeLong diagram
Welding: With moderated energy input per unit of length
Post-weld treatment: Solution heat treatment, where necessary
Remarks: Keep away from oil and grease, clean painstakingly after welding, use
stainless steel brushes
Martensitic chrome steels
Weldability: limited
Preheating: 250°C to 450°C (in function of composition)
Postweld treatment: Slow cooling to 120°C (martensitic transformation) and
annealing at 750°C or hardening (generally 1000°C/oil) and tempering (generally
750°C).
Watch for formation of chromium carbide between 500°C and 650°C!
Safety: Arc welding
see chapter safety
For further information, on-site training, technical advise or project management, please do not hesitate to
contact us.
|