We promote savings-through-repair welding.
Easy access to repair procedures allows spares optimisation and reduces down state costs.
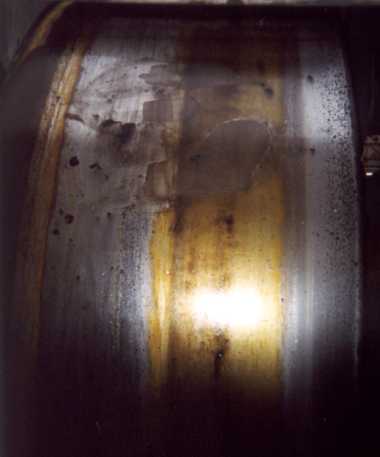
Support roll, cement kiln: heavy wear from surface fatigue
Repair involves the welding of dissimilar materials.
Arc welding processes - Dilution
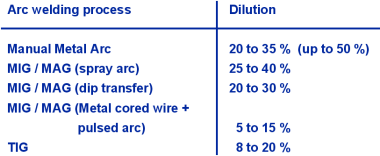
Common arc welding processes for repair welding
Heterogeneous welding
In most cases repair welding involves the welding of dissimilar materials.
When welding dissimilar materials, the dilution factor must always be taken into consideration.
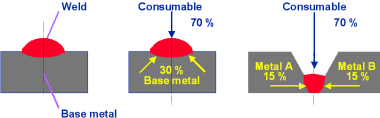
Dilution for Manual Metal Arc Welding
Repair welding of heavy steel components
Schaeffler diagram
The Schaeffler diagram indicates the approximate microstructure for high alloyed steel welds.
High alloy steels contain alloying elements as Ni, Mn, Cr, Mo, Nb, W, V, Cu.
The total percentage of all alloying elements is higher than 5%.
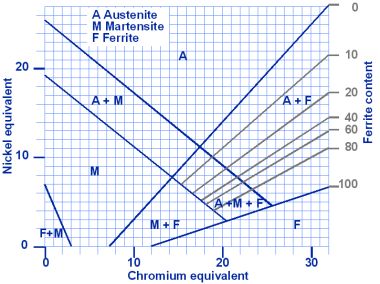
Schaeffler diagram
Chromium equivalent is calculated using the weight percentage of ferrite stabilising elements:

Nickel equivalent is calculated using the weight percentage of austenite stabilising elements:

The relative stabilising strength of each element is indicated by the coefficient in the equation.
Cold cracking
Cold cracking or hydrogen-induced cracking are terms for the
same phenomena. Well-known types of cold cracks are the
underbead crack (base metal), root crack, microcrack or transverse crack in the weld metal.

Cold cracking in the weld
Martensitic structures have together with the presence of hydrogen and residual stresses a tendency to cold cracking.
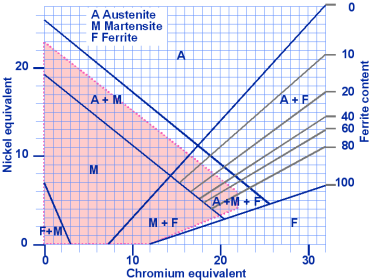
Schaeffler diagram, area of cold cracking
Cracks usually appear during cooling below 200°C.
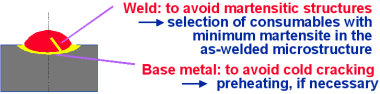
Cold cracking
Hot cracking
Austenitic structures have a tendency to hot cracking
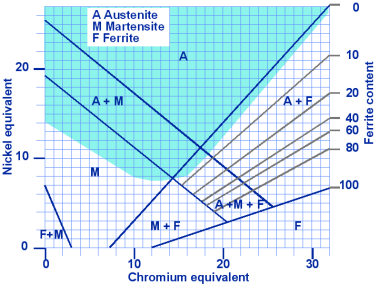
Schaeffler diagram, area of hot cracking
Hot cracking occurs slightly above the melting temperature of the lowest melting constituent.
At this moment in the welding solidification process, dendrites are surrounded by regions containing interdendritic low-melting liquid.
Strain causes fracture of the solid bridges.
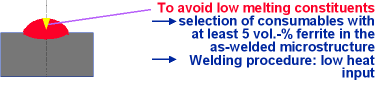
Hot cracking
Keep away from oil and grease, clean painstakingly after welding, use stainless steel brushes.
Intermetallic phase embrittlement: Sigma phase
Intermetallic phases (Sigma phases) may form at temperatures between 500 and 900°C in ferritic stainless steels containing
more than 14% Cr.
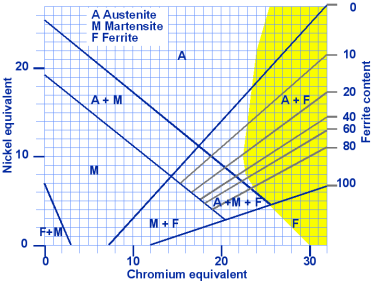
Schaeffler diagram, area of intermetallic phase embrittlement
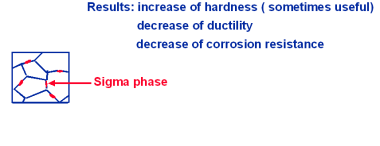
Intermetallic phase embrittlement: Sigma phase
Repair welding of cast iron components
see chapter Cast iron - Repair Welding
Safety: Arc welding
see chapter safety
For further information, on-site training, technical advise or project management, please do not hesitate to
contact us.
|