We promote savings-through-dependability improvements of your equipment and components.
The word dependability means ability of a system (asset) to perform a required function under given conditions for a given time interval (including failures and maintenance).
Dependability includes three major aspects:
- Reliability performance: ability of a system (asset) to perform a required
function under given conditions for a given time interval (including failures but
not maintenance, e.g. time between failures)
- Maintainability performance: ability to maintain or restore functions, e.g. duration
of the maintenance actions
- Supportability performance: ability of a support organisation of having the
right support (personnel and competency, tools, spare parts, etc.) at the necessary
place to perform the required maintenance activity at a given instant of time or
during a given time interval
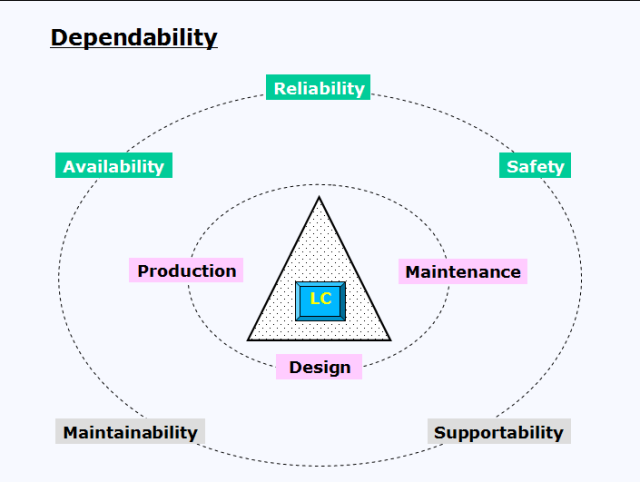
Positioning of dependability
Sources:
IEC 56/60300-3-14.Ed. 1
EN 13306: 2001
Dependability analysis
Failure rate prediction
Failure rate prediction of components.
The estimation may be based on:
- tests
- comparison to similar components
- experience from the field
At the end it should be possible to calculate the failure rate
of the complete system (asset).
System dependability analysis
For a system (asset) the dependability and the reliability can be
calculated or analysed from the failure rate of each component.
The structure of the system is described in a block diagram which
shows the system (asset) from the perspective of dependability or
reliability.
Failure Mode and Effect Analysis (FMEA)
FMEA is another approach to determine the impact of component failures.
The consequences on the component and the entire system are described.
The analyse can be qualitative or even quantitative depending on the
purpose of the analyse.
If system failure can occur as a result of a combination of several
failures, other methods must be considered.
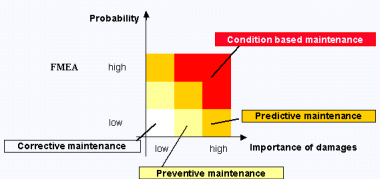
Failure Mode and Effect Analysis (FMEA)
Fault tree analysis (FTA)
FTA is a method for analysing complex failure situations. It gives good
understanding of dependencies and how failures occurs.
FTA is used in Probabilistic Safety Analysis (PSA).
Maintenance Need Analysis (MNA)
For all failing systems or components, maintenance is a key factor.
Regardless of how maintenance is performed questions like which tools
and test equipment, which training and support are needed will rise up.
Repair-discard analysis
Systems (assets), subsystems or components which fail can either be
repaired or discarded. In the repair-discard analyse are considered
both technical and economic aspects. This analyse must kept up to date
during the entire life-time.
Technical aspects consider the possibility to repair.
The economical aspects covers e.g. man-hours, equipment, spare parts,
storage, transportation, outsourcing and administrative costs.
The analyse shows which alternative would be the best solution.
Level of Repair Analysis (LORA)
LORA is designed for systems, subsystems or components needing maintenance.
It covers preventive and corrective maintenance. The word "level" indicates
on which level maintenance and repair should be performed: e.g. by the operators,
dedicated maintenance personnel, specialised maintenance workshops or by
suppliers.
The objective is to describe different alternatives and their costs
(e.g. for training, acquiring of maintenance resources, supervision, spare parts, tools, test equipment, etc.)
LORA is useful in larger organisations (airlines, transport companies,
cement or mining industry and car industry).
In the field of heavy maintenance and repair LORA is a very helpful tool for optimising spare part costs in function of operational consequences.
Spares optimisation
Often, spares are the largest part of maintenance costs. The aim should be
to find a cost-effective assortment of repairable spares to fulfil
dependability requirements such as operational availability.
Life Cycle Profit / Life Cycle Cost analyse (LCP / LCC)
The aim of this approach is to achieve a more cost-effective system (asset).
Life Cycle Profit / Life Cycle Cost analysis are very important as they gathers
information from other analyses and focus on economical aspects. Inventory costs
are includes in the Life Cycle Costs.
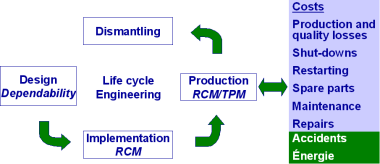
Life Cycle Management
Life Cycle Profit / Life Cycle Cost analysis consider the system (asset) and
the necessary support. Often it becomes evident that few of the cost elements
represent the major part of the actual costs. This gives a hint on where to
focus in order to achieve highest cost-effectiveness and sustainability
with design or dependability improvements.
For further information, on-site training, technical advise or project management, please do not hesitate to
contact us.
|