Anwendungen
Die Schweissverfahren MIG / MAG werden für Verbinden (Neuteile und Instandsetzung) und Beschichten (vorbeugend auf Neuteilen oder instandsetzend in Form von Aufbau und Beschichten) angewendet.
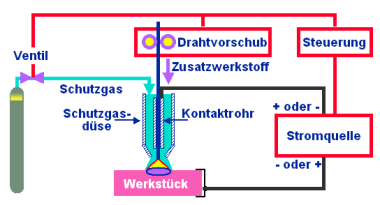
MIG / MAG Schweissverfahren
Zusatzwerkstoffe
Als Zusatzwerkstoffe stehen Volldrähte, Fülldrähte ohne Schlacke oder
Fülldrähte mit Schlacke zur Verfügung.
Lagerhaltung der Zusatzwerkstoffe
Kontinuierlichen Elektroden sind beim Lagern vor Verunreinigungen, Oxidation, Rostbildung etc. zu schützen.
Entsprechende Schäden stören bei der Drahtförderung und beim Stromübergang im Kontaktrohr.
Schäden durch unsachgemässe Behandlung und Lagerung verursachen Unstetigkeiten in der Draht- und Stromzufuhr.
Die Qualität wird somit schlecht beeinflussbar. Oxideinschlüsse und Porositäten sind das Resultat.
Vorbereitung der Werkstücke
- Für optimale Resultate werden verschlissene Teile vor dem
Schweissen gereinigt und mechanisch vorbereitet.
- Gebrauchte Teile können beschädigt sein und ermüdete Zonen aufweisen.
Ermüdungsrisse können Verunreinigungen enthalten.
- Beschädigte Zonen werden mechanisch oder durch Ausnuten entfernt.
- Es ist wichtig, dass alle ermüdeten und verunreinigten Zonen entfernt werden.
- Scharfe Kanten werden abgerundet (dies verhindert lokale
Überhitzung und unkontrollierten Einbrand).
Schweissbrenner
Durch das Schlauchpaket werden dem Schweissbrenner der Schweissstrom, der
Zusatzwerkstoff, das Schutzgas und gegebenenfalls das Kühlmedium zugeführt.
Der Schweissstrom wird in der Brennerspitze über einen gleitenden Kontakt
(im Kontaktrohr) auf den Zusatzwerkstoff übertragen. Schweissbrenner
bis 300 A können gasgekühlt werden. Ab 300 A ist eine Wasserkühlung notwendig.
Die Schutzgasdüse und das Kontaktrohr sind zu reinigen und mit geeigneten
Trennmitteln zu behandeln, damit ein Anhaften von Spritzern
möglichst verhindert wird.
Schutzgase
Die Wahl des Schutzgases beeinflusst folgendes:
- Temperaturverteilung im Lichtbogen
- Lichtbogenkennlinie
- Lichtbogenstabilität
- Lichtbogenform und Tropfenübergang
- Einbrandverhältnisse
- Nahtgeometrie
- Porenanfälligkeit
- Mechanische Eigenschaften
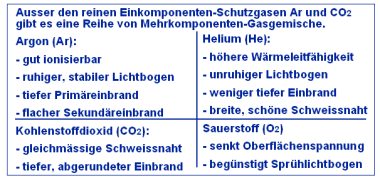
Einfluss der Schutzgaskomponenten im Mischgas
Parametereinstellung
Kurzschluss- und Sprühlichtbogen:
- Wahl der Schweissspannung an der Stromquelle.
- Regulieren der Drahtzufuhr über das Potentiometer für die Drahtgeschwindigkeit, regulierbar
von 0 bis 10, 15, 20 oder mehr m/min.
Der Motor für den Drahtvorschub ist stufenlos regulierbar.
Die Drahtgeschwindigkeit bleibt allerdings beim Schweissen konstant.
Der Schweissstrom wird von der Stromquelle automatisch reguliert. Der Lichtbogen wird dadurch stabilisiert.
- Induktivität für Schweissen mit Kurzschlusslichtbogen:
Optimale Schweissbedingungen liegen vor, wenn die Eigenfrequenz des Stromkreises auf die Kurzschlussfrequenz
abgestimmt ist.
- Bei zu hoher Induktivität wird die Tropfenbildung behindert.
- Bei zu kleiner Induktivität steigt der Strom beim Kurzschluss zu hoch (Spritzerbildung) und gleichzeitig geht
die Spannung gegen Null (der Lichtbogen muss neu gezündet werden).
- Induktivität für Schweissen mit dem Sprühlichtbogen:
Die Induktivität wird auf Minimal eingestellt, damit sich im Lichtbogen ein dynamisches Gleichgewicht einstellen kann.
Impulslichtbogen:
- Wahl der Parameter für die Impulsspannung an der Stromquelle
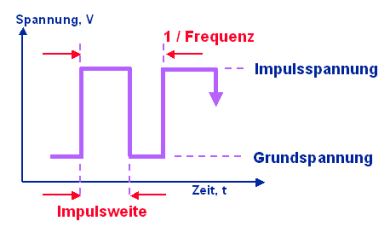
Impulslichtbogen: Parameter für Impulslichtbogen
- Die Grundspannung ist notwendig für das Erhalten des Lichtbogens in der Kaltphase. Typische Werte: min. 10 V, 20 A ).
- Die Impulsspannung produziert die Stromimpulse. Je höher die Stromimpulse sind, je mehr Wärme geht ins Schweissbad
über. Typische Werte: max. 40 V, 500 A ).
- Impulsweite: Eine grössere Impulsweite ergibt zusätzliche Wärme in das Schweissbad und beeinflusst das Abschmelzen
(Tropfengrösse). Typische Werte: 1 bis 15 ms.
- Frequenz: Eine höhere Pulsfrequenz ergibt zusätzliche Wärme in das Schweissbad; die Anzahl der übergehenden Tropfen
wird ebenfalls erhöht. Typische Werte: 30 bis 300 Hz.
- Drahtvorschub: Der Drahtvorschub beeinflusst primär die Abschmelzleistung. Höherer Vorschub verlangt höhere
Schweissstrommittelwerte (Pulsfrequenz).
Regulieren des Drahtvorschubs über das Potentiometer für die Drahtgeschwindigkeit, regulierbar
von 0 bis 10, 15, 20 oder mehr m/min.
Der Motor für den Drahtvorschub ist stufenlos regulierbar.
Die Drahtgeschwindigkeit bleibt allerdings beim Schweissen konstant.
Der Schweissstrom wird von der Stromquelle automatisch reguliert. Der Lichtbogen wird dadurch stabilisiert.
- Die Induktivität wird auf Minimal (Null) eingestellt.
Zur perfekten Ausbildung des Impulslichtbogens darf im Sekundärstromkreis keine zu hohe Induktivität vorhanden sein. Schweissstromführende Kabel (Massekabel oder Verbindungsschlauchpakete zwischen Stromquelle und Drahtvorschubgerät) sollen deshalb nie einfach gerollt resp. aufgewickelt werden.
Das Massekabel ist möglichst parallel zu den Schlauchpaketen zu verlegen. Der Abstand zwischen beiden ist so klein wie möglich zu halten.
Für mehr Information oder technische Beratung,
bitte kontaktieren Sie uns.
|